Nationalism, workers’ power, and the myth of auto tariffs
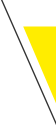
Shawn Fain and the UAW have come out in favor of Trump’s tariffs. They’re giving presentations to support their position that free trade is bad (fair enough) and using the narrative that NAFTA killed manufacturing jobs and auto jobs in particular. “The auto tariffs are designed for a specific purpose: they raise the cost on the companies that have killed good jobs in a race to the bottom for cheap labor elsewhere while Wall Street makes a killing,” says Fain. But this is working off the myth that “we don’t make anything in the US anymore.”
Fain focuses on excess capacity in domestic auto assembly. He suggests that tariffs are uniquely capable of forcing auto executives to redistribute profits to workers—without explaining how. Leaving aside the reality of what Trump’s tariffs are and that we’re not being transported back in time to 1990, I don’t think this makes sense on its own terms. More importantly, it misses the real threats to autoworkers and the role the union can play in resisting them.
First, the US auto industry continues to produce millions of consumer vehicles—about 11 million a year in 2023. In the “golden age” of the UAW, let’s say 1960, it was 7.9 million. NAFTA went into effect in 1994; auto employment rose from 1.1 to 1.4 million until 2001, with that year’s recession and as 9/11 further stalled the auto market. Roughly 200,000 auto workers were laid off, lowering the number of autoworkers to about 1.1 million through 2007.
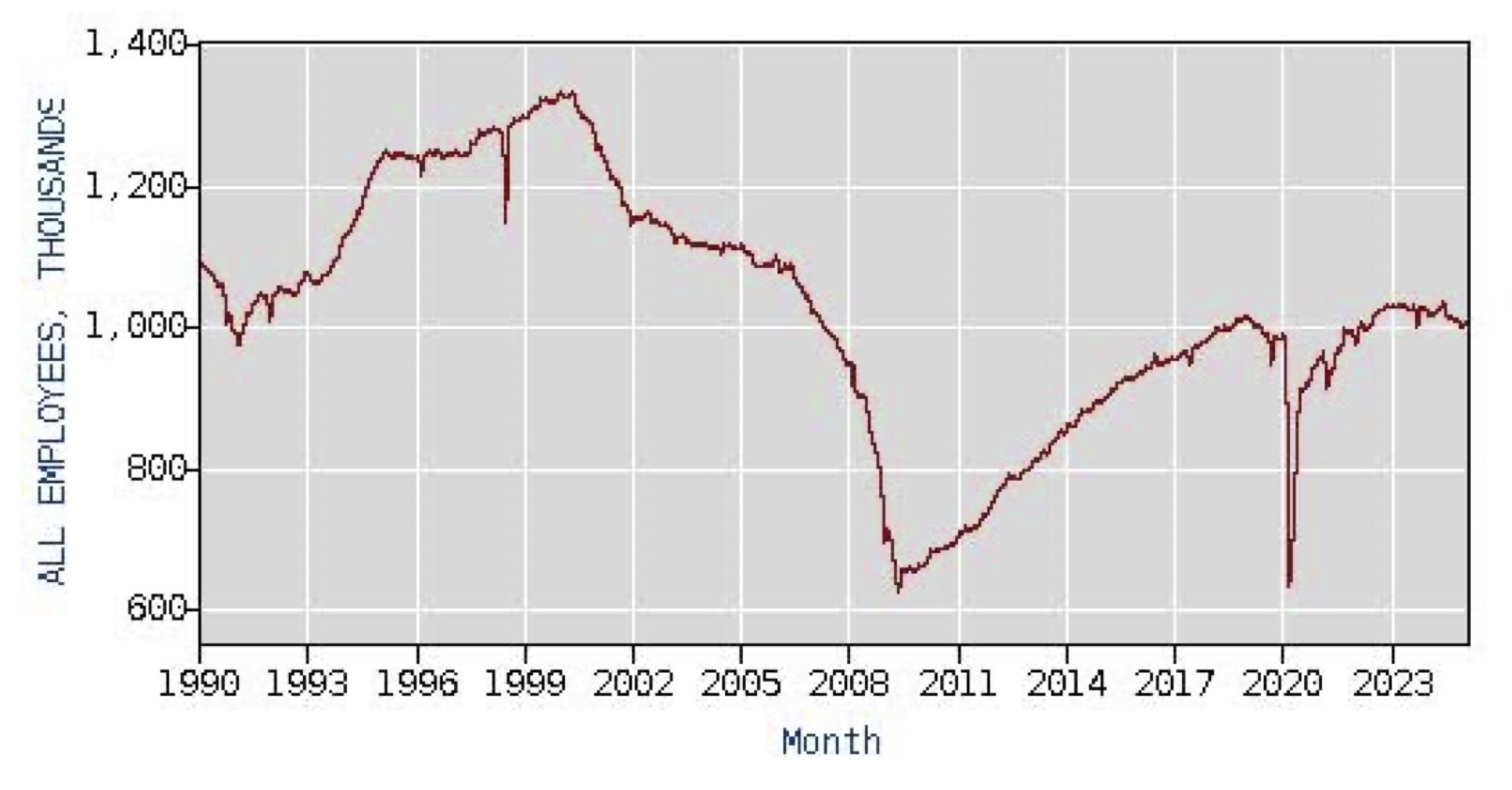
The most significant hit to auto employment was in 2008 due to the financial crisis. 600,000 jobs were eliminated—half of all auto workers employed at the time. It took nearly a decade to slowly tick employment back up to a million workers.
The Great Recession did more than eliminate auto jobs. The Bush Administration conditioned its bailouts to auto companies on enormous concessions from the UAW. Herman Rosenfeld, a retired autoworker in Canada, explained, “The United Auto Workers (UAW) had to match the wage, benefit, and working condition levels at the U.S. operations of Honda, Nissan, and Toyota.”
According to Sam Gindin, former Research Director of the Canadian Autoworkers (CAW):
By no later than February 17, 2009, the Company shall submit to the President’s Designee … [a] term sheet signed on behalf of the Company and the leadership of each major U.S. labor organization [essentially the UAW] that represents the employees.” Over and above the elimination of any layoff benefits above customary severance pay—something the union had already conceded—the terms called for a reduction in workers’ wages, benefits and working conditions to match “no later than December 31, 2009” levels that are “competitive with the average as certified by the Secretary of Labor” at the U.S. operations of Nissan, Toyota, and Honda.
The federal government led an attack on the auto workers’ union, as they did in 1979 when Jimmy Carter’s administration gave loans to Chrysler while demanding wage cuts from the union. The union ultimately failed to fight the terms of the loans in 2008 and the state succeeded in cutting thousands of jobs, retiree health care, and “replacing current workers with entry-level employees . . . making $14 an hour in wages.”
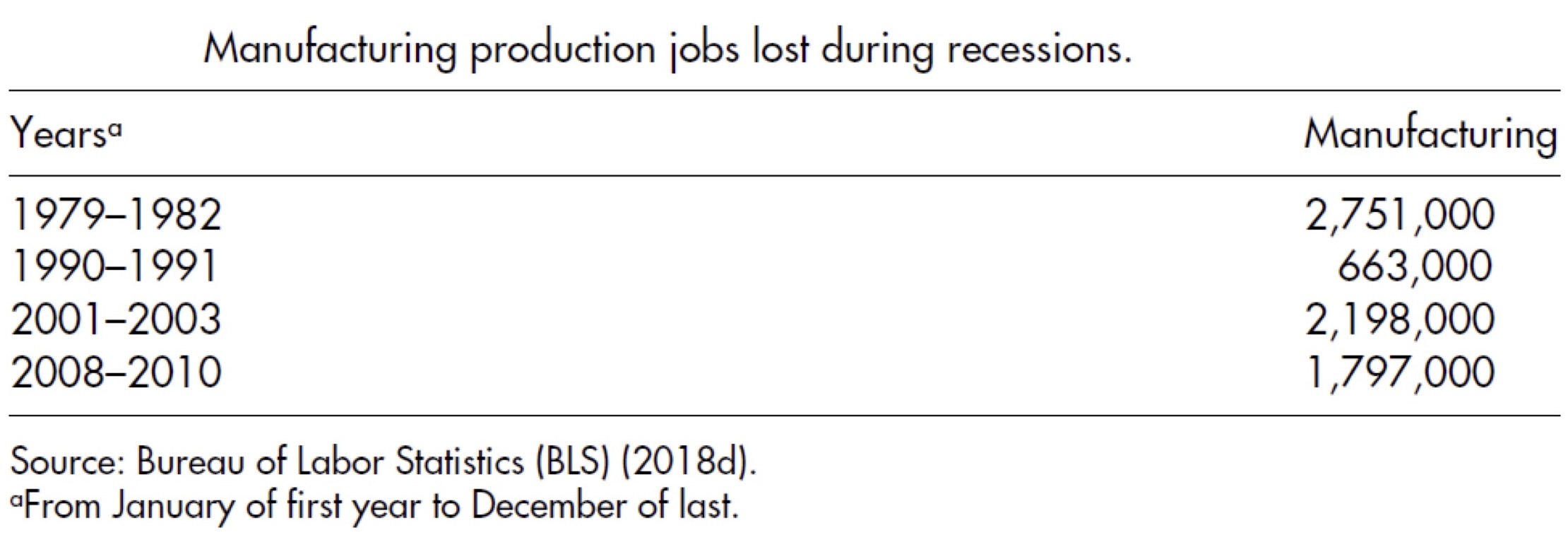
The auto industry still produces millions of cars, and according to the Bureau of Labor Statistics (BLS), has roughly the same number of auto workers employed as there were in 1992. The number of union jobs has declined. Why?
Jobs weren’t so much offshored as they were sped up and moved South. The US South. Michigan still has the most autoworkers in the country, but there has been an enormous move to Alabama and Kentucky, where there are no unions. The graph below shows that in 1990 there were practically no manufacturing workers employed in auto in Alabama. In 2023, Alabama was the fourth largest state employing auto workers (23,000); Kentucky was the third largest employer with 24,000 workers. That’s not counting parts manufacturing, which accounted for another 30,000 and 34,000 workers, respectively.
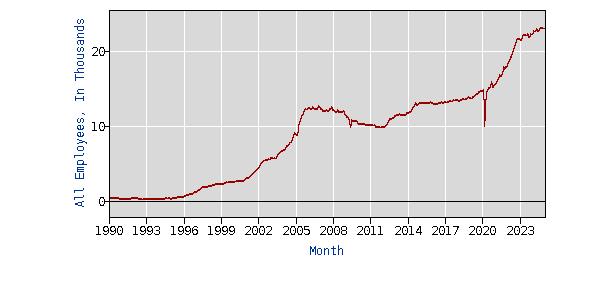
Productivity increases (“speed up”) ate at new job growth. Up through the Great Recession, manufacturing productivity rose by an average of 4 percent annually. These productivity gains were less automation and more labor reorganization. Kim Moody, writing in the journal Class & Capital, analyzed the rise of “lean production” in manufacturing:
The major driving force behind increased labour productivity from the early 1980s to 2007 just before the Great Recession has been capital’s aggressive campaign of work intensification. This offensive has included the introduction of lean production methods with their “constant improvement” in worker performance; the Just-In-Time (JIT) acceleration of the labour process (“management-by-stress”) and the pace of supply chain networks; related work intensification programmes such as Total Quality Management that aid in filling in the pores of the work day; alternative work schedules with 10-hour shifts that maximize the productivity curve; the simultaneous introduction of Human Resource Management with its “performance assessments”; the reduction in break time; and more recently, the many digital and biometric forms of workplace surveillance, work measurement and algorithm-driven work patterns.
In sum, auto jobs have been most threatened by productivity gains that are the direct result of ceding control of the production process, recessions that have used crises to restructure the industry, and direct attacks by the state. If the union were to address any of these issues, it would mean that they would have to target the auto companies, fight for control of the shop floor, and even buck the state. This would require a concerted campaign to claw back management rights, attack speed-up, and politically win concessions from the employers to create jobs. Organizing unorganized plants would have to definitively break from labor-management partnerships that primarily benefit the company and adopt an “us and them” approach to labor relations. Focusing on NAFTA (a trade deal more than 30 years past) has meant aligning with the Trump administration and the domestic auto industry, even as Fain rightfully denounces the abduction of its members and the attacks on federal employees.
Opinions expressed in signed articles do not necessarily represent the views of the editors or the Tempest Collective. For more information, see “About Tempest Collective.”
Featured Image credit: Joe Ross; modified by Tempest.
Categories
We want to hear what you think. Contact us at editors@tempestmag.org. And if you've enjoyed what you've read, please consider donating to support our work:
DonateAndy Sernatinger View All
Andy Sernatinger is a labor organizer and member of the Tempest Collective in Madison, Wisconsin.